Mit dem Crashversuch, der für die letzte Woche im Juli geplant ist, nähert sich das Forschungsprojekt „CraCpit“ seinem Höhepunkt. Dabei wird gleichzeitig überprüft, ob das entwickelte Simulationsmodell die Realität korrekt abbildet, wie auch ob die designten Sicherheitselemente das Überleben eines Aufpralls ermöglichen.
Im Rahmen des Projekts wurde ein FEM-Simulationsmodell für Faserverbundwerkstoffe so erweitert, dass damit möglicherweise auftretendes Strukturversagen präziser abgebildet und besser vorhergesagt werden kann. Um die Korrektheit der entworfenen Methode zu validieren, wird eine computerberechnete Simulation in der Realität nachgestellt und die Ergebnisse der Simulation mit Messungen aus der Realität verglichen. Mittels zweier Kräne wird der Versuchsrumpf ähnlich einer Schaukel aufgehangen und tritt unter einem Einschlagwinkel von 45° sowie einer Geschwindigkeit von 20m/s gegen den Betonboden an.
Die Akaflieg Hannover bereitet hierfür einen Flugzeugrumpf vor und stattet diesen mit den im Projekt designten und berechneten Nachrüstelementen aus. Diese Elemente sollen sicherstellen, dass dem Piloten im Falle eines Crashs ein Überlebensraum erhalten bleibt und er den Unfall lebendig überstehen kann.
Um Komplikationen zu vermeiden und den Versuch möglichst unkompliziert halten zu können, wird kein vollständiges Flugzeug verwendet, sondern nur ein Rumpf. Beide Tragflächen und selbst Seiten- sowie Höhenleitwerk nehmen nicht am Crashversuch teil. Für sie springen Ersatzmassen ein, für die es nun Aufnahmen zu konstruieren und zu fertigen gilt. Infrage kommt beispielsweise eine Stahlrohrkonstruktion, auf die Hantelgewichte aufgesteckt werden könnten.
Ebenfalls zu entwerfen ist ein Konzept zur Aufhängung des Rumpfes an die Kräne. Dabei muss darauf geachtet werden, die Struktur des Versuchskörpers nicht zu verändern. Eine Versteifung die weder in noch fliegenden Flugzeugen desselben Typs, noch der Simulation vorhanden ist, würde den Versuch naheliegenderweise verfälschen. Wichtig ist, dass die Aufhängung bis zum Aufprall intakt bleibt und den Rumpf im vorgegebenen Winkel aufschlagen lässt.
Vor dem Einbau der Nachrüstelemente müssen diese selbstverständlich hergestellt werden. Für die Fertigung wird eine Negativ-Form aus feinporigem Hartschaum gefräst und verwendet. Aktuell ist geplant, die Elemente im Handlegeverfahren samt anschließendem Vakuumpressen herzustellen. Der optimale Schichtaufbau, Belegeplan genannt, muss dazu noch ermittelt werden, denn die mechanischen Eigenschaften der Elemente hängen maßgeblich vom Schichtaufbau und der verwendeten Gelege- bzw. Gewebeart ab.
Die prinzipielle Idee sieht vor, dass die Struktur sukzessive versagt und dadurch die kinetische Energie des Aufpralls aufnimmt. Die auftretende Beschleunigung sowie die Zeitdauer der Verzögerung ist fest, es kann also nur Einfluss auf den Verlauf der Beschleunigung genommen werden. Hohe Beschleunigungen sind tödlich, besonders Beschleunigungsspitzen müssen vermieden werden. Optimal ist also, die auftretenden Beschleunigungskräfte vom Aufprall bis zum Stillstand möglichst konstant zu halten, gewissermaßen gleichmäßig auf die zur Verfügung stehende Zeitspanne zu verteilen.
Aktuell ist der Crashrumpf entkernt und für den Einbau der Nachrüstelemente bereit. Diese werden mit angedicktem Epoxidharz in den Cockpitbereich des Rumpfes eingeklebt. Die Dicke des Harzes soll dabei an keiner Stelle mehr als 3 mm betragen. Um diese Genauigkeit zu erreichen, wurde der Rumpf zu Projektbeginn vermessen und ein digitales Modell erstellt. Um eventuelle Reparaturstellen oder bisher unerkannte Defekte aus dem früheren Leben des Rumpfes erkennen zu können, wurde der Lack bereits abgetragen.
Unmittelbar vor dem Crashversuch wird der Versuchskörper mit Messtechnik ausgestattet. Zur Verfügung stehen 32 Kanäle die von zwei Inertialmesseinheiten (IMU) und zahlreichen Dehnungsmessstreifen (DMS) belegt werden. Die IMUs werden im Schwerpunkt angebracht. Mit ihnen wird überprüft, ob der Aufschlag im korrekten Winkel und korrekter Geschwindigkeit stattgefunden hat. Die Messwerte der DMS werden mit den vorhergesagten Werten der Simulation verglichen. Stimmen diese überein, kann das Simulationsmodell als korrekt angesehen werden und für die Konstruktion zukünftiger Bauelemente verwendet werden.
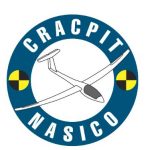